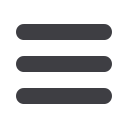
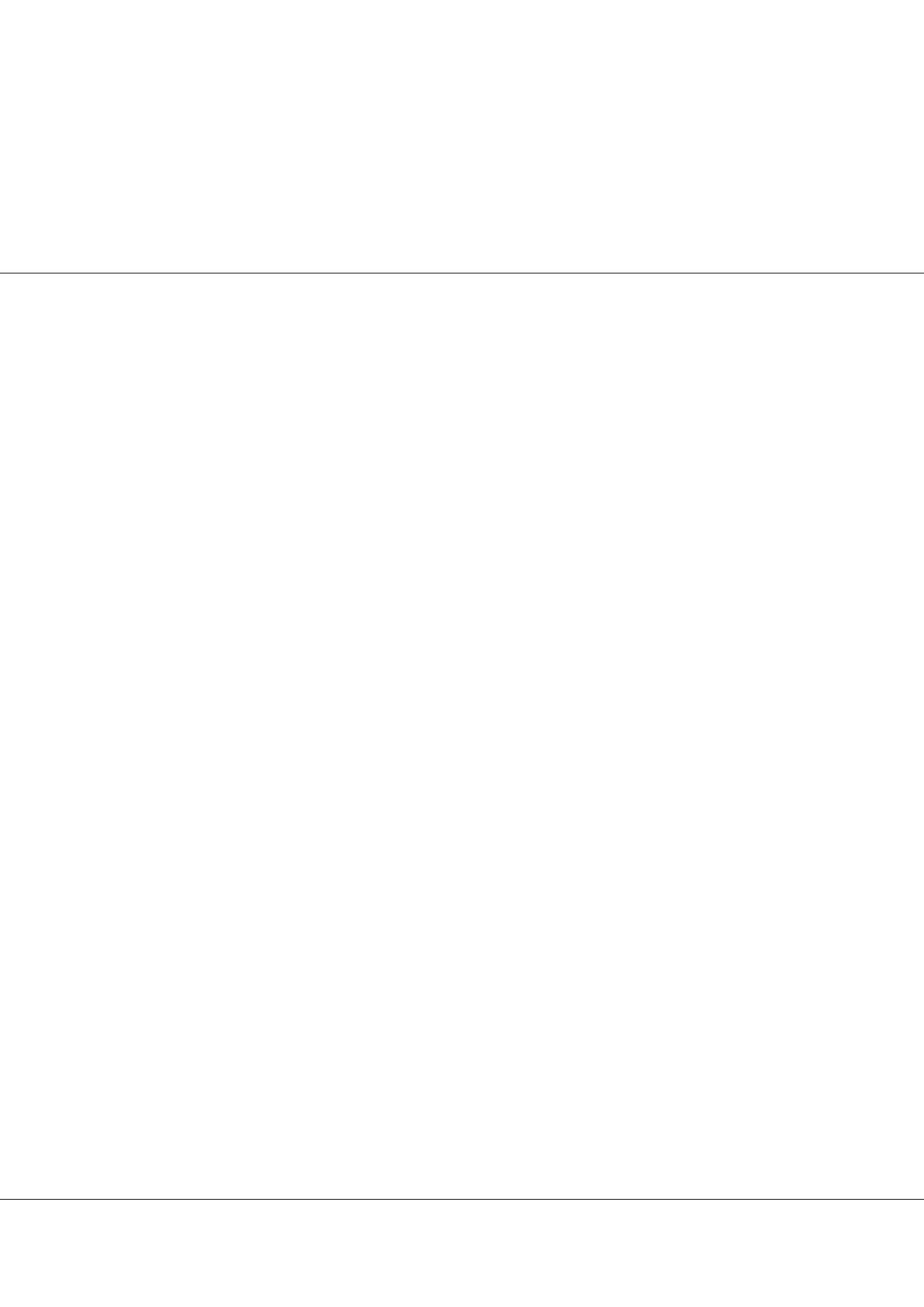
Volume 5, Issue 2(Suppl)
Adv Automob Eng 2016
ISSN: 2167-7670, AAE an open access journal
Page 60
Automobile 2016
December 01-02, 2016
conferenceseries
.com
Automobile Engineering
December 01-02, 2016 Valencia, Spain
2
nd
International Conference and Exhibition on
Adv Automob Eng 2016, 5:2(Suppl)
http://dx.doi.org/10.4172/2167-7670.C1.006Fitness-for-service and residual stress analysis for automotive powertrain components using neutron
diffraction
Dimitry Sediako
1
, Frank Czerwinski
2
, Wojciech Kasprzak
2
, Ravi Ravindran
3
and
Anthony Lombardi
3
1
Canadian Nuclear Laboratories, Canada
2
CanmetMATERIALS, Canada
3
Ryerson University, Canada
T
he industry-wide push to develop advanced, low-displacement, high power density engines frequently demands increased
operating temperatures and pressures for the powertrain components, such as engine heads, cylinder blocks, pistons, etc. At
the same time, lightweighting has led to increasing use of aluminum alloys in these components. Both trends inevitably result in
demand for higher-performing aluminum alloys and in the need to develop and test new alloying systems. An
in-situ
study of the
creep behavior using neutron diffraction quickly reveals the response of individual crystallographic planes to the applied load under
the operating-engine temperatures. This knowledge helps to identify the alloy chemistry and processing conditions that result in
manufacturing engine components capable of sustaining the thermal mechanical loads over the expected life cycle of a vehicle, which
typically exceeds 3000 hours. Residual stress in the as-cast engine components and efficient stress mitigation are further ongoing
concerns for many OEMs. A series of neutron studies has been performed at the Canadian Nuclear Laboratories to evaluate how
heat treatment techniques affect stress profiles along the cylinder web areas in engine blocks and between valve seats in aluminum
engine heads. These studies have revealed the most critical information about the residual stress for development of manufacturing
technologies that prevent distortion or cracking in the powertrain components.
dimitry.sediako@cnl.caDistributed solar network for air ventilation in the hybrid vehicles
Aly Aboulnaga
King Faisal University, KSA
I
t is very important to manage the power generation in the hybrid vehicles to maintain the highest possible efficiency. One of the
most effective methods to increase the efficiency of the hybrid vehicle is use of auxiliary power sources for temporary loads inside
and outside the vehicles. This allows the main energy source(s) to be used only to drive the vehicle and therefore increase the driven
mileage. This paper presents a distributed solar network on the external body of the vehicles. The output of this solar network is
connected to a buck-boost power DC-DC converter. This scheme is used to drive a ventilation system mainly to avoid temperature
rise inside the vehicle especially in summer or when parked in sunny climate. This will reduce the degradation of the interior of the
vehicle and help the air-conditioning to run effectively. The excess energy produced by this scheme is used to charge the main battery
bank of the hybrid vehicle. A quantitative study of this distributed solar network will be presented to show the improvement in the
overall efficiency and the lifetime of the vehicle.
aaboulnaga@kfu.edu.sa