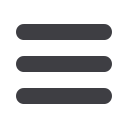
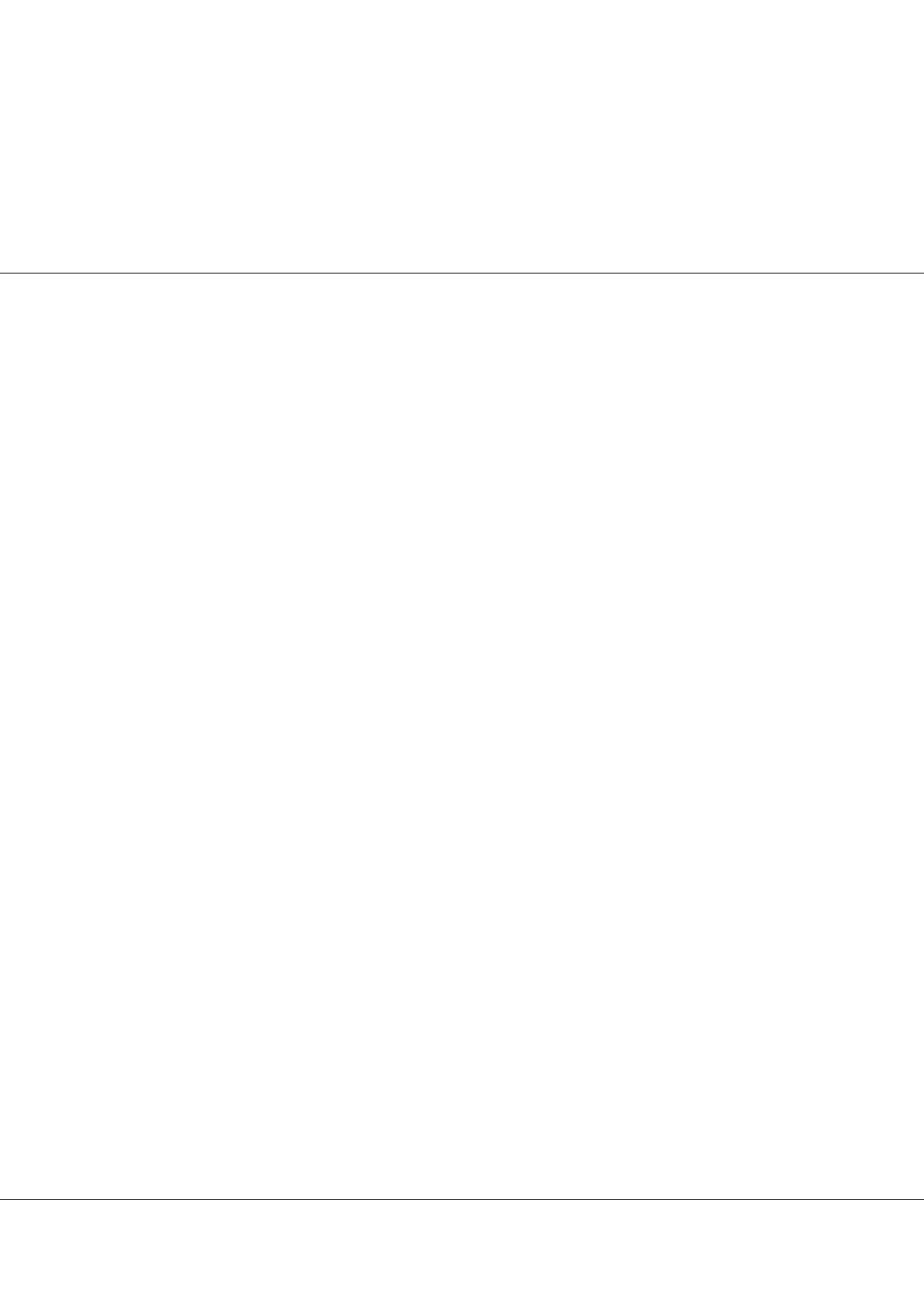
Volume 5, Issue 2(Suppl)
Adv Automob Eng 2016
ISSN: 2167-7670, AAE an open access journal
Page 64
Automobile 2016
December 01-02, 2016
conferenceseries
.com
Automobile Engineering
December 01-02, 2016 Valencia, Spain
2
nd
International Conference and Exhibition on
Adv Automob Eng 2016, 5:2(Suppl)
http://dx.doi.org/10.4172/2167-7670.C1.006Design, analysis and fabrication of an automotive F-N-R gearbox with spur-gear differential
K G Sachin
Amrita Viswa Vidyapeetham, India
P
ower transmission is an inevitable part in any automobile. The power from the prime mover (engine/motor) is transferred to the
wheels using a suitable transmission system. Various designs of gearbox have been developed in the past. In this paper, an F-N-R
(forward-neutral-reverse) gearbox with a compact spur-gear differential is designed by following the design parameters for spur gear,
for the required output torque of a vehicle. All the gears and casing for the gearbox is modeled using Solidworks tool. A simple and
user-friendly shifting mechanism is designed for the gearbox, adding to comfort. A new spur-gear differential is designed, having
spur gears to accomplish differential action, which is more compact and light-weight compared to a conventional differential, since
the heavy bevel gear assembly is omitted. Different analyses such as static, dynamic (time-dependent), contact, modal and fatigue
analyses are done using ANSYS software. The main objective is to design and fabricate a light-weight, efficient and compact F-N-R
gearbox as a replacement to current models.
kgsachin94@gmail.comMotor torque control algorithm to prevent rollover for in-wheel drive electric vehicle
Kangneoung Lee, Hyunjong Ha, Sungbae Jeon
and
Hyunsoo Kim
Sungkyunkwan University, Korea
I
n this study, an in-wheel motor torque control strategy was proposed for a 4-wheel drive in-wheel type electric vehicle by
considering the rollover risk, vehicle driving and handling performance. LTR (lateral load transfer ratio), which is the rollover
index, is significantly relevant to the vehicle lateral acceleration. For reducing the rollover risk, the vehicle lateral acceleration must
be decreased. Lateral acceleration depends on the vehicle speed and turning radius. These factors can be controlled by the in-wheel
motor torque control. To develop the in-wheel motor torque control strategy, the LTR was calculated from the vehicle dynamics to
estimate the rollover. Threshold of LTR was introduced using the vehicle specifiations. LTR error which is the difference between the
threshold of LTR and actual LTR was used to control the front and rear motor torques. Motor control strategy was composed of two
parts: First, to reduce the vehicle velocity, output torque of the in-wheel motors at all wheels were reduced depending on the amount
of the LTR error. In addition, co-operative braking control was performed using the electro-hydraulic braking system. Second, to
improve the handling performance, additional output torque control of the front in-wheel motors were carried out. Through the
simulation results, it was found that the rollover risk was decreased as much as 30% by the in-wheel motor torque control compared
to that of no control.
eehoa12381@gmail.com