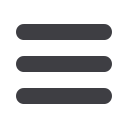
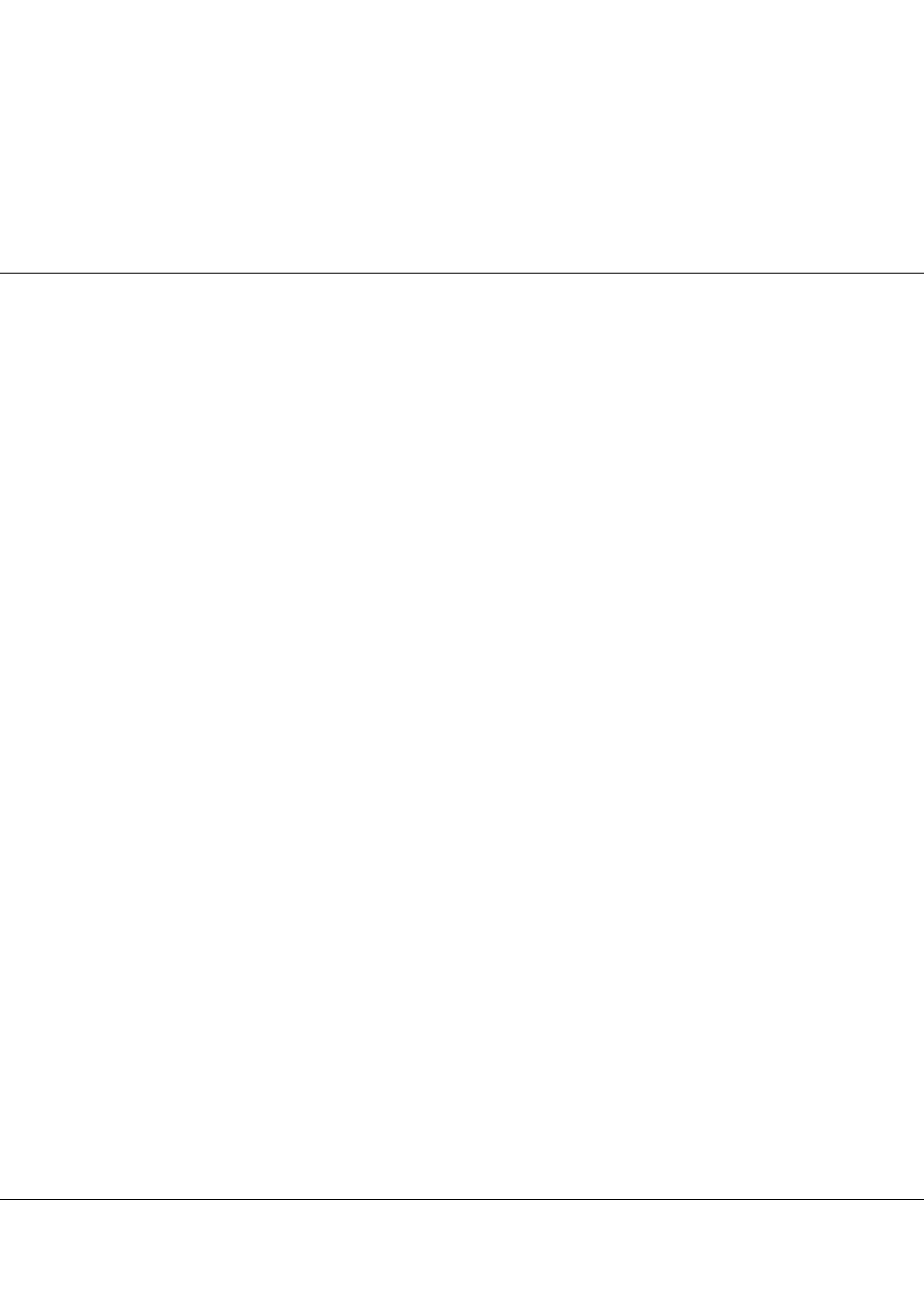
Volume 5, Issue 2(Suppl)
Adv Automob Eng 2016
ISSN: 2167-7670, AAE an open access journal
Page 58
Automobile 2016
December 01-02, 2016
conferenceseries
.com
Automobile Engineering
December 01-02, 2016 Valencia, Spain
2
nd
International Conference and Exhibition on
Adv Automob Eng 2016, 5:2(Suppl)
http://dx.doi.org/10.4172/2167-7670.C1.006Design of communize mounting system for 3 cylinder petrol and 4 cylinder diesel engine
Aniket Palasgaonkar
Tata Technologies, India
T
his paper describes powertrain mounting stiffness calculation which gives communize outer geometry for petrol and diesel
powertrain and two different stiffness sets by achieving desired target of elastic and torque roll axis alignment and mode
decoupling. First petrol 3 cylinder engine powertrain mount and stiffness is finalized by six degree of freedom calculations; next
diesel four cylinder engine powertrain stiffness is relatively changed with respect to petrol stiffness such that to achieve desired
target. Primary reasons for two sets of stiffness for petrol and diesel powertrain are weight, number of cylinder and inertia property
difference. Lastly, both achieved stiffness are checked from manufacturing feasibility and accommodated in same mount outer
geometry and checked in layout for packaging constraint. Same outer mount geometry helps maintain modularity, reduce FEA and
packaging lead time and cost.
aniketpalasgaonkar@gmail.comMnCr-materials for new chassis lightweight concepts
Barbara Homann
Outokumpu EMEA GmbH, Germany
F
orta H, Outokumpu has developed a special material exclusively for automotive applications. This material combines good
formability with high strength, where the strength increases further during the forming process. These properties enable new
lightweight concepts. The alloy design of the new lightweight material is based on an austenitic microstructure. During forming, this
austenitic structure provides the formation of so-called “twins” and thus to increase the strength of the material enormously. Hence,
the good formability can be ideally combined with a high strength. Traditional materials such as aluminum or carbon steels do not
show this effect. The material is called “Forta H” and is industrially available. The base material “Forta H500”, named after its yield
strength, has a tensile strength of over 900 MPa with an elongation after fracture of more than 50%. By hardening, the grades “Forta
H800” and “Forta H1000” can be achieved. The strengths of this special material increase during the forming process and in case of
a crash. The material, developed for automotive applications, is widely tested and available on an industrial scale. It is offered in sheet
thicknesses of t=0.5 mm to t=4.0 mm and a width up to b=1350 mm, where additional dimensions are conceivable. The presentation
will provide an overview of the features and benefits of the new ultra-high- strength grades of Outokumpu. In this regard, a variety
of results, such as weldability, formability, fatigue behavior, and corrosion resistance will be shown. Finally, some applications will be
presented.
barbara.homann@outokumpu.com