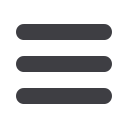
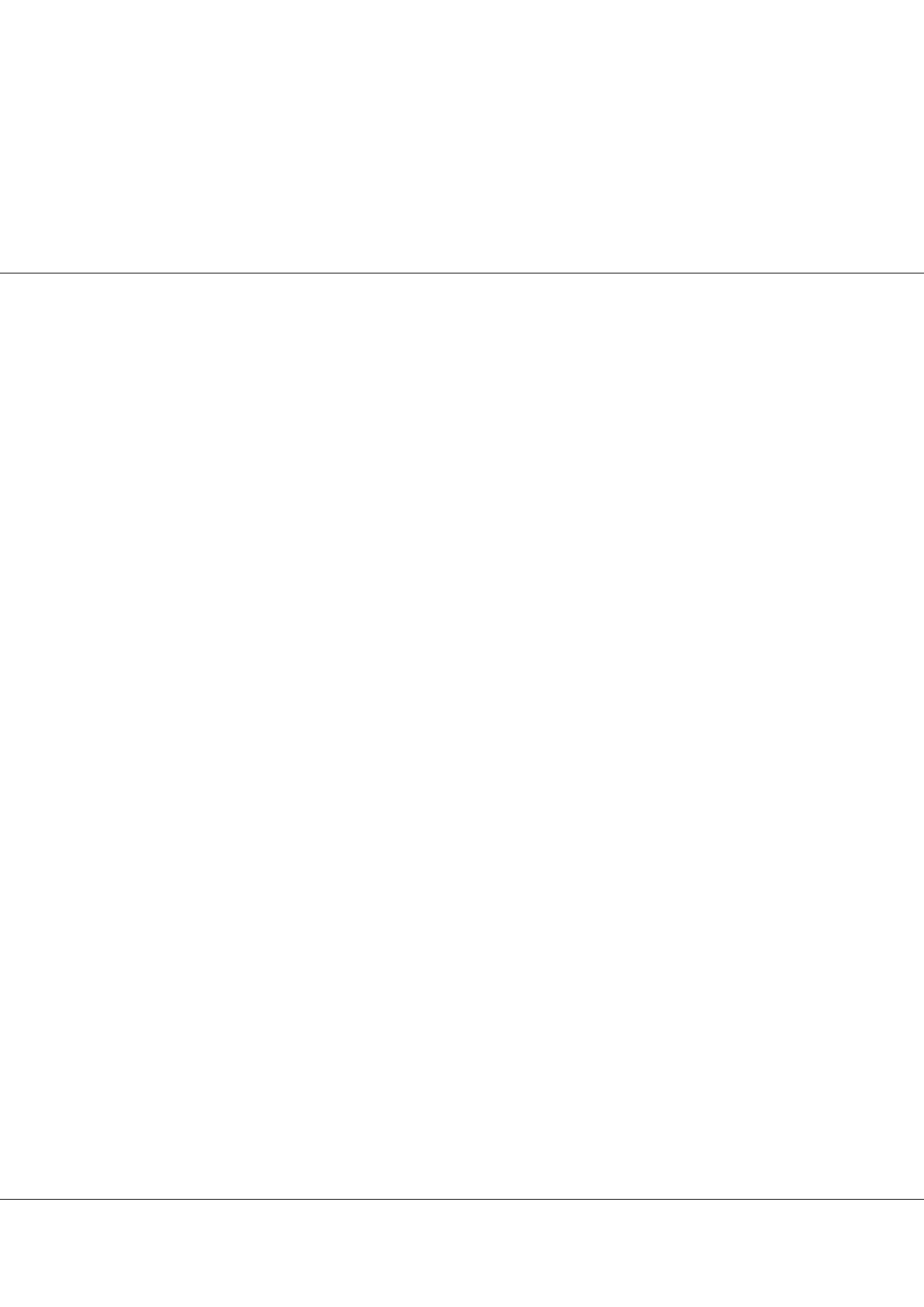
Volume 5, Issue 2(Suppl)
Adv Automob Eng 2016
ISSN: 2167-7670, AAE an open access journal
Page 63
Automobile 2016
December 01-02, 2016
conferenceseries
.com
Automobile Engineering
December 01-02, 2016 Valencia, Spain
2
nd
International Conference and Exhibition on
Adv Automob Eng 2016, 5:2(Suppl)
http://dx.doi.org/10.4172/2167-7670.C1.006Design, development and validation of new engine head cover with advanced sealing system by using
simulation tools
Jham Kunwar Tikoliya
Volvo Eicher Commercial Vehicle LTD, India
T
he existing head cover is having external oil and blow by separation unit, which is not only costlier but also complex and leads
to increase in the overall height of engine which was difficult to integrate in new variants of vehicles. Existing head cover sealing
system was also not foolproof and with slight variation in part dimensions, there were high chances of leakage. A new head cover
has been designed with internal baffle type oil and blow by separation system to ensure efficient separation and proper packaging of
the system in new varients. The new system has been finalized after 26 DOEs of different wire mesh sizes and different baffle plate
size and positions. The final system has two bowl shaped separation units with wire mesh with two cup type oil separation passages
and one baffle plate for separating blow by. The system works on condensation and gravity method. The blow by is guided through
a well-defined passage integrated in aluminum cylinder head cover itself. The blow by passage angle is decided to ensure minimum
oil flow with blow by. The new seal has been designed with the head cover to ensure no oil leakage during engine running. The seal
compression has been controlled by introducing a metal cup in bush and stopper assy which is used to ensure uniform compression
of the seal. The metal cup controls the rubber bush compression which indirectly controls the compression of the seal. The complete
head cover with advanced sealing system has been validated rigorously for durability, oil consumption; leakages, vibrations and oil
carry over and have been proved a better solution over the existing design. Same methodology can be benchmarked for the other
existing engine variants.
jktikoliya@vecv.inThermodynamic cycle analysis of mobile air conditioning system using HFO-1234yf as an alternative
replacement of HFC-134a
Jignesh Gohel
1
and
Ragesh Kapadia
2
1
Aditya Silver Oak Institute of Technology, India
2
SVMIT College, India
T
his paper presents thermodynamic cycle analysis of mobile air conditioning system using HFO1234yf as alternative replacement
for HFC-134a. Under a wide range of working conditions (varying condensing temperature, evaporating temperature, sub cooling
and sub heating with internal heat exchanger (IHX) and without internal heat exchanger) on simple vapor compression system, we
compare the energy performance of both refrigerants - R134a and HFO1234yf. Result shows that without using an internal heat
exchanger, at lower condensing temperature (35
o
C), mass flow rate increases about 27-32%, refrigerating effect decreases 22-25%,
compressor work increases 4-6% and COP decreases about 3-5%. While at higher condensing temperature (55
o
C), mass flow rate
increases about 35-42%, refrigerating capacity decreases 27-30%, and compressor work increases 8-13% and COP decreases 7-10%.
Using an internal heat exchanger (IHX), these differences in the energy performance are significantly reduced. At lower condensing
temperature (35
o
C), mass flow rate decreases about 18-22%, refrigerating capacity decreases 15-18%, compressor work increases
1-3% and COP decreases about 2-3%. At higher condensing temperature (55
o
C), mass flow rate decreases 23-28%, refrigerating
capacity decreases 18-22%, compressor work increases 5-8% and COP decreases about 4-7%. The energy performance parameters
of HFO1234yf are close to those obtained with HFC-134a at low condensing temperature and making use of an IHX. Even though
the values of performance parameters for HFO1234yf are smaller than that of HFC-134a, but difference is small so it can be a good
alternative to HFC-134a because of its environmental friendly properties with introducing IHX.
Jigneshgohel.me@Socet.edu.in