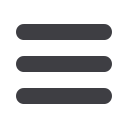
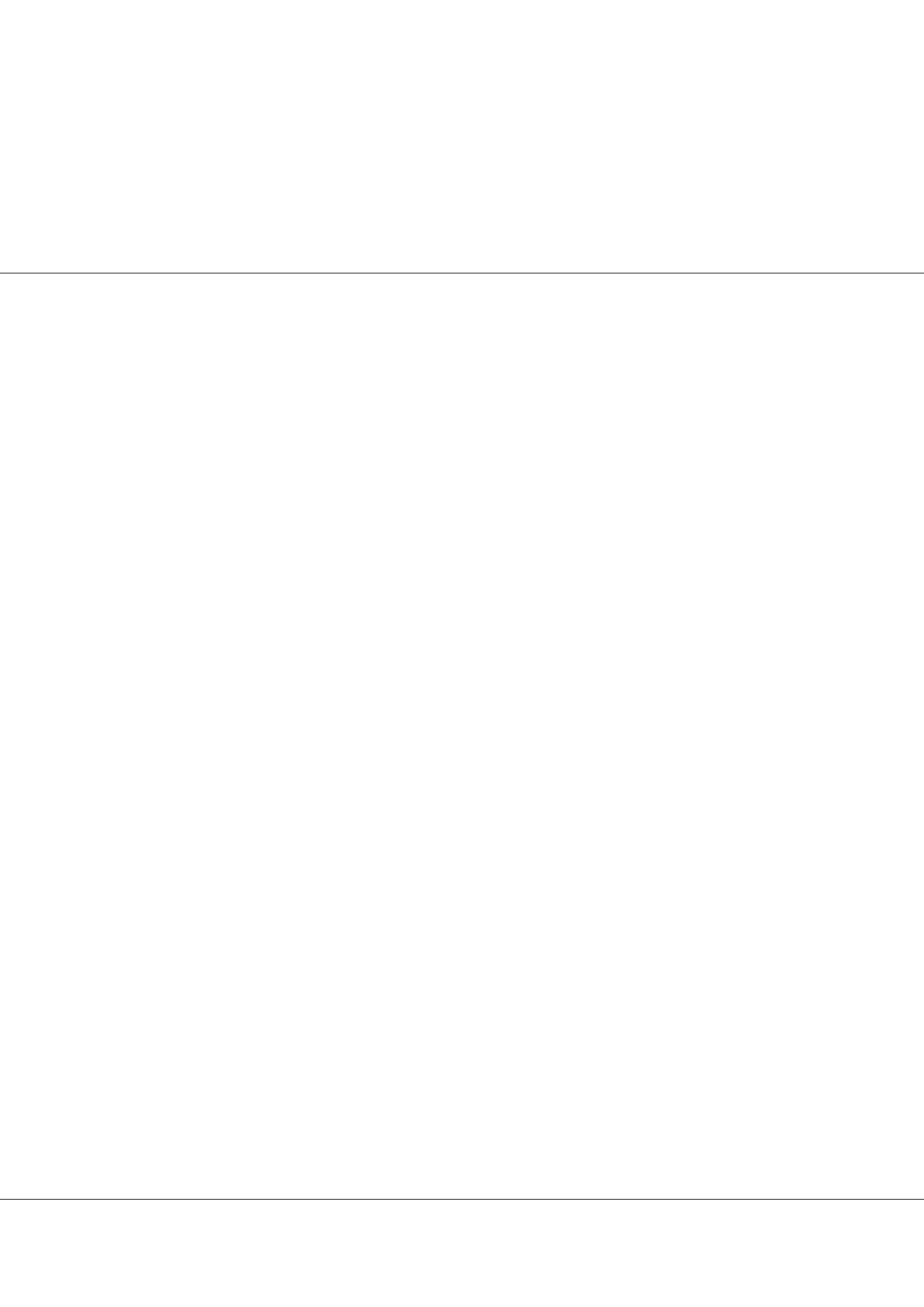
Volume 5, Issue 2(Suppl)
Adv Automob Eng 2016
ISSN: 2167-7670, AAE an open access journal
Page 69
Automobile 2016
December 01-02, 2016
conferenceseries
.com
Automobile Engineering
December 01-02, 2016 Valencia, Spain
2
nd
International Conference and Exhibition on
Adv Automob Eng 2016, 5:2(Suppl)
http://dx.doi.org/10.4172/2167-7670.C1.006A new paradigm for active suspension of vehicles
S B Phadke
College of Engineering Pune, India
G
ood passenger comfort, ride comfort and ride handling are sought after goals in modern cars. Passive suspension systems can
offer only a limited performance when meeting these goals. Well established and emerging feedback control strategies like
the sliding mode control, adaptive control, optimal control to name just a few, have found the problem of active suspension to be
an attractive application. Active suspension systems can outperform passive and semi active systems but bring new problems with
them with regard to ride and suspension safety. From a control point of view, suspension systems are uncertain systems affected by
an unknown disturbance in the form of an unknown road profile. In the literature, road preview using special sensors or using lead
vehicles in a convoy has been proposed by many researchers. Estimating the effect of unknown road profile and uncertainties without
using special sensors is made possible by two new methods called Inertial Delay Control (IDC) and Disturbance Observer (DO) is a
new paradigm that gives a remarkable performance. The estimation is made in real time with the help of measurement of sprung mass
position and velocity. The methods of IDC and DO are further developed to do away with velocity measurement which is a costly and
noisy affair, by developing the estimate using only the sprung mass position. The method of estimation is generalized to improve the
accuracy of estimation. A remarkable feature of the method is to get a performance that is better than sky-hook without having to
use a sky-hook damper. This talk develops the idea further to explore how the method can be employed to give ride comfort without
losing on handling requirements. The new methods are further developed to handle the conflict between improving ride comfort
and keeping the suspension stroke within the rattle space constraints. Comparisons are made with other prevailing methods like the
Linear Quadratic Regulator. Novel nonlinear functions combined with the methods of IDC or DO enable making the compromise
just when needed. The talk concludes by discussing future directions.
sbp.instru@coep.ac.inOptimizing the efficiency of a gasoline engine, using self generated hydrogen–By utilizing the engine’s
dissipating heat energy of gasoline generated power for generating a secondary fuel in the formof hydrogen
Shashwat Tripathi
JSS Academy of Technical Education, India
U
se of hydrogen as a fuel in IC engines has been supported for years, particularly because of it’s high combustion energy and power
output; besides the non-toxic emissions.However, the development and research of hydrogen based engines has always been
hindered by the issue of production and storage of hydrogen. In the context of our proposed hydrogen powered internal combustion
engine, the primary fuel for powering the engine is still gasoline but we are utilising the loss of gasoline generated power by generating
a secondary fuel in the form of hydrogen. A thermo-electric generator or a number of thermo-electric generators are employed on the
engine exhaust which converts the engine generated heat energy into electric power. This electric power is then used to electrolyze the
water to generate hydrogen. The hydrogen produced in the process is fed to engine, by blending it with gasoline supply, to re-use the
power, lost in the form of heat from the engine. Modern gasoline engines have a maximum thermal efficiency of about 25% to 30%
when used to power a car. In other words, even when the engine is operating at its point of maximum thermal efficiency, of the total
heat energy released by the gasoline combustion, about 70-75% is rejected as heat without being turned into useful work. By using
thermo-electric generators this power is recycled and used as a power source for carrying the electrolysis of water for the production
of HHO gas. This gas is then blended (1-2% by Volume) with the air/fuel mixture and fed to the engine cylinder for combustion. The
engine performance parameters (fuel consumption, thermal efficiency, power, etc.) now get enhanced by a significant amount. Also,
reduction in amount of unburned hydrocarbons, CO-CO2 emissions, etc., is achieved.
trips_93@yahoo.co.in