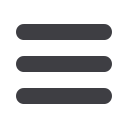

Volume 5, Issue 2(Suppl)
Adv Automob Eng 2016
ISSN: 2167-7670, AAE an open access journal
Page 68
Automobile 2016
December 01-02, 2016
conferenceseries
.com
Automobile Engineering
December 01-02, 2016 Valencia, Spain
2
nd
International Conference and Exhibition on
Adv Automob Eng 2016, 5:2(Suppl)
http://dx.doi.org/10.4172/2167-7670.C1.006Performance comparison of half and full toroidal traction drive CVTs
Rathindranath Maiti, Kumar Shanu
and
Vineet Sahoo
Indian Institute of Technology, Kharagpur, India
T
oroidal CVT is an ideal automotive transmission system in terms of simplicity, fuel economy and performance. It consists of
two discs forming a toroidal cavity and a power roller enclosed in a casing containing lubricant at very high pressure. In order
to get the CVT with lesser mechanical losses, efficiencies of full-toroidal and the half-toroidal drives are estimated analytically. The
present investigation aims at establishing the design guidelines for the geometry and dimension parameters of this CVT layout for
uniform axial loading and optimal ratio range. First a kinematic analysis is done in order to find the speed ratios followed by the
dynamic analysis where forces on different parts are analyzed. For estimating the torque losses through the bearings, the SKF model
for the frictional torque calculation (in case of ball /roller bearing) or hydrodynamic lubrication theory (in case of journal bearing),
is used. These frictional torque losses are distributed among the input and output shafts depending upon the ratios of the final input
and output torque. A fully developed isothermal fluid film contact model between the discs and rollers, based on the results of EHL
theory, is used to evaluate the slip and spin losses. With this method, the traction coefficient and slip can be predicted within 10%
accuracy which makes the optimum control of the normal force of the power transmitting contact of a toroidal CVT. The effects on
efficiency due to variation in traction drive parameters (half cone angle, cavity radius, fluid property) are also found out.
rmaiti@mech.iitkgp.ernet.inA novel four wheel vehicle
Santiranjan Pramanik
and
S S Thipse
Symbiosis International University, India
A
new arrangement of wheel location has been considered for a four wheel vehicle so that the turning radius can be reduced
greatly. The front axle is to use one wheel only instead of two wheels of a conventional vehicle. The middle axle is to use two
wheels and the rear axle is to use one wheel. The single wheels of the front and rear axle will be placed at the mid position so that
the arrangement becomes symmetrical. This arrangement helps us to follow the law of correct steering for all angular positions. The
steering mechanism will be such that the front and rear wheels will rotate equal amount but in opposite directions. A crossed four bar
mechanism has been used to rotate the front and rear wheel while the vehicle is taking a turn. The rotation of each wheel will be 30
degree and the maximum steering error is 0.2 degree only. The wheels on the middle axle will not be rotated due to steering but are
connected to the differential gear box to transmit motion. The intersection of the front and rear wheel axis will be always on the axis
of the middle axle. Hence pure rolling will take place while the vehicle is taking a turn. The design enhances the life of the tires and
parking of this vehicle will be easier. Each wheel of the middle axle shall have two tires so that it can bear more load and increases
stability of the vehicle while taking a turn.
santiranjan_pramanik@rediffmail.com